Projekt Adatai
Projekt azonosító:
2018-1.3.1-VKE-2018-00041
Projekt címe:
Intelligens, prediktív szerszámfelügyeleti eljárások kidolgozása és rendszer kialakítása, valamint a fejlesztés fenntartására alkalmas kutatási együttműködés létrehozása
Projekt költsége:
1 569 249 800 Ft
Támogatási összeg:
1 181 409 675 Ft
Konzorciumvezető:
“KÁTA CNC” Ipari és Kereskedelmi Kft.
Konzorciumi tagok:
Óbudai Egyetem
Megvalósítás időtartama:
2018.12.01 – 2021.11.30.
Projekt rövid összefoglalója
A “KÁTA CNC” Kft. mint konzorcium vezető, az Óbudai Egyetemmel és a Szent István Egyetemmel közösen 1.181 millió forintot meghaladó vissza nem térítendő támogatást nyert el a „Versenyképességi és Kiválósági Együttműködések” című pályázati kiíráson. Az 1.569 millió forintot meghaladó összköltségvetésű beruházásból a jelenlegi szerszám diagnosztikai rendszereknél fejlettebb, komplexebb, adaptív rendszer kifejlesztése valósul meg.
A forgácsoló megmunkálás hatékonyságának növelését a forgácsolószerszám kihasználtságának maximalizálásával lehet megoldani. A CNC forgácsoló gépek a kihasználtság növelésének hatékony eszközei. A szerszámok kihasználtságának maximalizálása azonban egy határon túl a szerszám károsodása miatt a hatékonyságot csökkenti. Ideális esetben egy szerszám legjobb kihasználtsága, annak tönkremeneteléig tart. A kritikus idő (a tönkremenetel pillanata) előtt cseréljük. Ha korábban cseréljük, akkor a szerszámot nem használtuk ki és ehhez az elméleti ideális állapothoz képest fajlagosan drágább a szerszám és fajlagosan több a hulladék (I. típusú veszteség).
Ha a kritikus pontot túllépjük, akkor a szerszámot ugyan kihasználtuk, de a tönkrement szerszámmal selejt darabot gyártunk és ez lesz a veszteség, ami szintén drágább fajlagos gyártást és több fajlagos hulladékot jelent, különösen nagy értékű (kritikus) munkadarabok és technológiák esetében (II. típusú veszteség).
A jelenlegi diagnosztikai rendszerek a szerszámok tönkremenetelét képesek felismerni, de nem képesek előre jelezni, így az ideális kihasználást nem lehet megvalósítani.
Célunk egy olyan, a jelenlegi rendszereknél fejlettebb, komplexebb, adaptív rendszer kifejlesztése, amely a szerszámok tönkremenetelét képes előre jelezni, és még a szerszámtörés, illetve a selejt termék gyártása előtt beavatkozni.
A javasolt rendszer, a szerszámról és környezetéről, érzékelők segítségével kapott jelek alapján javasol módosításokat, illetve meghatározza a várható kritikus meghibásodási időpontot.
Az előbbiek specifikusan kialakított ipari informatikai rendszeren keresztül csatolhatók, a konkrét alkalmazásokhoz. A megbízható eredmények elérése érdekében vizsgálni kell a külső szenzorokkal (hang/akusztika, hőmérséklet és hőeloszlás, sebesség, forgácsalak) a beépítésre kerülő “szenzormentes” (áramfelvétel, rezgés) és a kettő ötvözésével történő állapotfelügyeletet. Külön hangsúlyt fektetünk a rezgésméréssel történő hibaesemény megelőzésére (pl. frekvenciaváltozás) és ennek kiterjesztésére más bejövő adatok összevetésével (pl. rezgésmérés és a főorsó áramfelvétel mérésének ötvözése). Fókuszba kerülnek a gyakorlatban általánosan használt CNC gép vezérlések és CAM rendszerek, ahol a kézi és CAM programozáson belül is vizsgáljuk a szerszám-szerszámgép rendszerében beálló (pl. kinematikai) hibák csökkentési lehetőségeit (hirtelen irány és fogásmélység változások). Hipotézisünkben az előrejelzés több paraméter nagymennyiségű adatának az analízisét feltételezi, így valószínűsíthetően újszerű informatikai megoldások (gépi tanulás, neurális hálózatok, BigData elemzések) alkalmazása célszerű.
A szerszám tönkremenetele, mint mechanikai probléma modellezhető. Ez alapján megállapíthatók a terhelhetőségi határok pontos paraméterek mellett. A szerszámok valóságos geometriája, anyagminősége, hőkezelése nem tökéletesen egyforma, így a modellezés alapján megállapított paraméterek szórásának mérése szükséges. A mechanikai modell és a mérések alapján a szerszámok terhelhetősége, valóságos tűrésekkel megállapítható. Az egyes szerszámgépek, mint a szerszámok „peremfeltételei” szintén nem ideális, tökéletes kényszereket jelentenek. A fellépő deformációk, a mozgó alkatrészek játéka, a befogás tökéletlensége szintén befolyásolja a tönkremenetelt. A hatások megállapítása, fontossági sorrendje, elhanyagolhatósága szükséges eredmény a diagnosztikai rendszer összeállítása során.
A jelenlegi diagnosztikai rendszerek két fő érzékelési módot alkalmaznak, direkt és indirekt módszert. Az új rendszert, a meglévő módszereket alapul véve, két irányban lehet fejleszteni. Az egyik lehetőség új paraméterek, új típusú érzékelők bevezetése. A másik lehetőség az érzékelők adatainak új típusú feldolgozása, amely komplex rendszerként tekint az érzékelők és adatok összességére. A kutatás során az öntanuló mesterséges intelligencia alkalmazásának lehetőségét is megvizsgáljuk, alkalmassága esetén a rendszer elemévé tesszük.
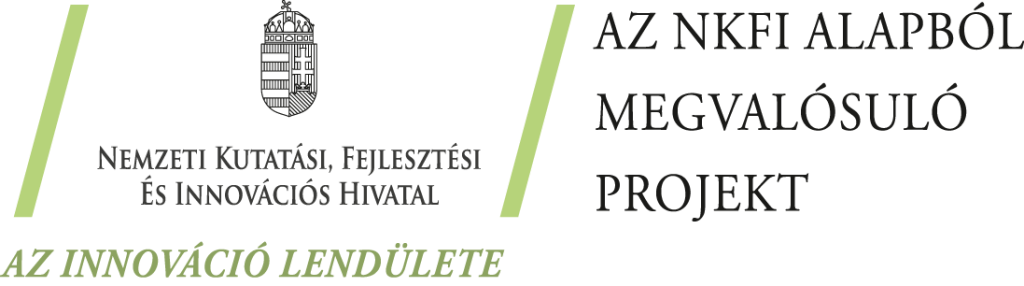
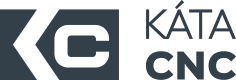
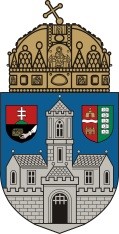
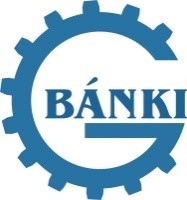